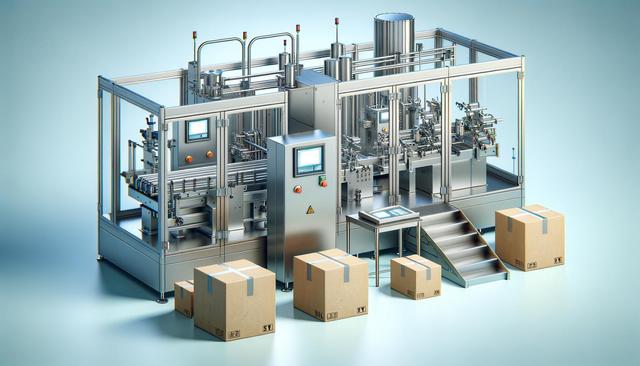
Understanding the Role of Packaging Machines in Modern Manufacturing
The Evolution of Packaging Machinery
Packaging machines have come a long way from manual wrapping and boxing techniques. In the past, packaging was labor-intensive and prone to inconsistencies. With the introduction of automated systems, industries began to see improvements in both speed and reliability. Today, packaging machines are found in nearly every sector, including food and beverage, pharmaceuticals, cosmetics, and consumer electronics. These machines not only streamline production but also enhance product safety, shelf life, and branding.
The development of different types of packaging machines has allowed manufacturers to tailor their operations based on specific needs. From form-fill-seal machines to vacuum packaging and shrink wrapping units, there’s a solution for virtually every packaging challenge. The ability to automate repetitive tasks reduces human error and boosts overall productivity, which is especially important in high-volume environments.
Types of Packaging Machines and Their Applications
There are numerous types of packaging machines, each designed for specific tasks and industries. Understanding these variations can help businesses choose the right equipment for their needs. Some of the most common types include:
- Filling Machines: Used to dispense liquids, powders, or granules into containers.
- Sealing Machines: Ensure the product is securely enclosed, often used in food and medical packaging.
- Labeling Machines: Apply labels for branding, compliance, or tracking purposes.
- Wrapping Machines: Encase products in protective film or paper.
- Cartoning Machines: Package items into boxes or cartons for shipment.
Each machine type serves a unique role in the packaging process. For example, in the pharmaceutical industry, blister packaging machines are essential for safely enclosing pills and capsules. In contrast, beverage companies might rely heavily on capping and labeling machines to manage bottling lines efficiently.
Benefits of Automated Packaging Systems
Automated packaging systems offer a wide range of advantages that go beyond mere convenience. These include:
- Increased Efficiency: Machines can operate continuously, reducing downtime and speeding up production.
- Consistency and Quality Control: Automation ensures uniform packaging, which is crucial for brand image and customer satisfaction.
- Cost Savings: While the initial investment can be significant, long-term savings come from reduced labor costs and minimized waste.
- Enhanced Safety: Especially in food and pharmaceutical sectors, contamination risks are lowered with minimal human interaction.
These benefits make packaging machines a worthwhile investment for businesses aiming for scalability. Moreover, with growing demand for eco-friendly practices, many machines now support sustainable packaging materials, aligning with environmental goals.
Challenges and Considerations When Choosing Packaging Equipment
Despite their advantages, selecting the right packaging machine involves careful planning and consideration of several factors. One major challenge is the upfront cost, which can be a barrier for small to medium-sized enterprises. Additionally, compatibility with existing production lines and the flexibility to handle multiple product types are key concerns.
Companies must also consider:
- Machine footprint: Space availability on the production floor may limit equipment size.
- Maintenance requirements: Some machines require regular servicing to maintain efficiency.
- Operator training: Staff must be trained to use and troubleshoot the machines effectively.
- Regulatory compliance: Especially important in industries with strict packaging standards, such as medical or food sectors.
By addressing these considerations during the selection process, businesses can avoid costly adjustments later. Consulting with packaging specialists or equipment manufacturers can also provide valuable insights tailored to specific operational needs.
The Future of Packaging Machines
The future of packaging machines looks promising, with new technologies continuously improving performance and sustainability. Innovations such as smart sensors, robotics, and machine learning are making systems more adaptive and efficient. For example, modern machines can now detect errors in real-time, adjust settings automatically, and even predict maintenance needs before breakdowns occur.
Another growing trend is the integration of Internet of Things (IoT) technologies, which allow remote monitoring and data collection. This capability helps manufacturers optimize performance, reduce downtime, and make informed decisions based on real-time analytics. In addition, more focus is being placed on reducing the environmental impact of packaging operations by designing machines that work with recyclable or biodegradable materials.
As consumer demand continues to shift toward personalized and sustainable products, packaging machines must adapt. Flexible packaging systems that can handle various product sizes and shapes on the same line are becoming increasingly popular. These advancements not only meet market demands but also open new opportunities for innovation in packaging design and functionality.
Conclusion: Investing in Efficiency and Quality
Packaging machines play a critical role in modern manufacturing by improving efficiency, ensuring product safety, and supporting brand consistency. Whether you’re a startup or a large-scale producer, understanding the different types of machines and their capabilities can help you make informed decisions that align with your business goals.
By investing in the right packaging technology, companies can streamline operations, reduce costs, and meet the growing expectations of consumers and regulatory bodies. As technology continues to evolve, staying current with trends and innovations will allow manufacturers to remain competitive and responsive in a dynamic market landscape.