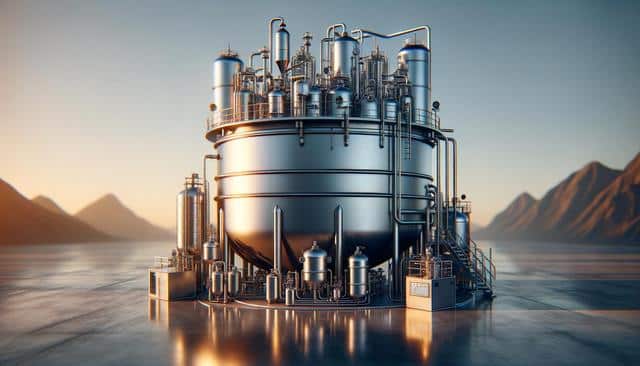
Understanding the Role and Design of Chemical Mixing Tanks
The Purpose and Importance of Chemical Mixing Tanks
Chemical mixing tanks are used in numerous sectors such as pharmaceuticals, agriculture, food processing, and water treatment. Their primary function is to mix chemical substances in a controlled environment to ensure uniformity, stability, and safety. These tanks are designed to handle a wide range of chemical properties, including corrosive, flammable, or reactive substances. By enabling seamless blending and agitation, they help in producing consistent chemical solutions that meet industry standards.
In industrial processes where precision is critical, chemical mixing tanks play a valuable role in quality control. For instance, in pharmaceutical manufacturing, active ingredients must be evenly distributed throughout a solution to maintain dosage accuracy. Similarly, in water treatment, chemicals like chlorine or fluoride need to be thoroughly mixed to ensure safe and effective purification. Without these tanks, achieving such consistency would be challenging and potentially hazardous.
Key Materials Used in Manufacturing
The materials used to manufacture chemical mixing tanks are chosen with durability and chemical resistance in mind. Common materials include stainless steel, polyethylene, polypropylene, and fiberglass-reinforced plastic. Each material offers specific advantages depending on the type of chemicals being handled and the operating environment.
Key considerations when selecting materials include:
- Chemical compatibility – to prevent corrosion or degradation.
- Temperature tolerance – especially important for exothermic reactions.
- Mechanical strength – to withstand pressure and agitation forces.
- Hygiene and cleanability – particularly in food-grade or pharmaceutical applications.
Stainless steel is often used for its strength and resistance to both heat and corrosion. Polyethylene and polypropylene are preferred for their lightweight nature and compatibility with a wide range of chemicals. Fiberglass-reinforced plastic offers excellent durability and is ideal for outdoor installations due to its UV resistance.
Types of Mixing Mechanisms
Mixing tanks can be equipped with various mechanisms that influence how substances are blended. The choice of mixing mechanism depends on the viscosity of the materials, the desired mixing speed, and the overall process requirements. Common types include:
- Paddle mixers – suitable for low to medium viscosity fluids.
- Turbine mixers – ideal for rapid mixing and emulsification.
- Anchor mixers – designed for high-viscosity substances.
- Static mixers – involve no moving parts and are used in continuous flow systems.
Each mixer type is paired with a motor or drive system that allows speed adjustments to match process needs. Advanced models may include programmable logic controllers (PLCs) for automated control, improving consistency and reducing manual intervention. Understanding how each mechanism operates helps users select the most efficient configuration for their specific application.
Safety and Compliance Considerations
Safety is a critical factor when dealing with chemical mixing tanks. These tanks must comply with industry regulations and standards to ensure they are fit for handling hazardous substances. Regulatory bodies may require specific testing and certification based on the tank’s intended use and the chemicals involved.
Important safety features can include:
- Pressure relief valves to prevent over-pressurization.
- Sealed lids and venting systems to manage fumes.
- Secondary containment systems to catch leaks or spills.
- Corrosion-resistant coatings for additional protection.
Operators should also be trained in the proper use and maintenance of these tanks. Routine inspections and monitoring are vital for early detection of wear, corrosion, or structural weakness. Investing in safety measures not only protects workers and the environment but also helps avoid costly downtime and legal liabilities.
Applications Across Industries
Chemical mixing tanks are indispensable across a wide range of industries due to their adaptability and functionality. In agriculture, they are used for preparing fertilizers and pesticides. In the cosmetics sector, they help blend lotions, creams, and other personal care products. The food and beverage industry relies on them for mixing flavorings, preservatives, and other additives.
In wastewater treatment, mixing tanks are essential for adjusting pH levels, removing contaminants, and ensuring proper chemical dosing. The oil and gas sector uses specialized tanks for blending fuels, additives, and lubricants. Each application requires a tailored solution to meet specific operational and regulatory requirements.
The versatility of chemical mixing tanks makes them a valuable asset for any business that works with liquid chemicals. Their ability to streamline processes, improve product quality, and maintain safety standards contributes significantly to operational efficiency and sustainability in chemical-related industries.